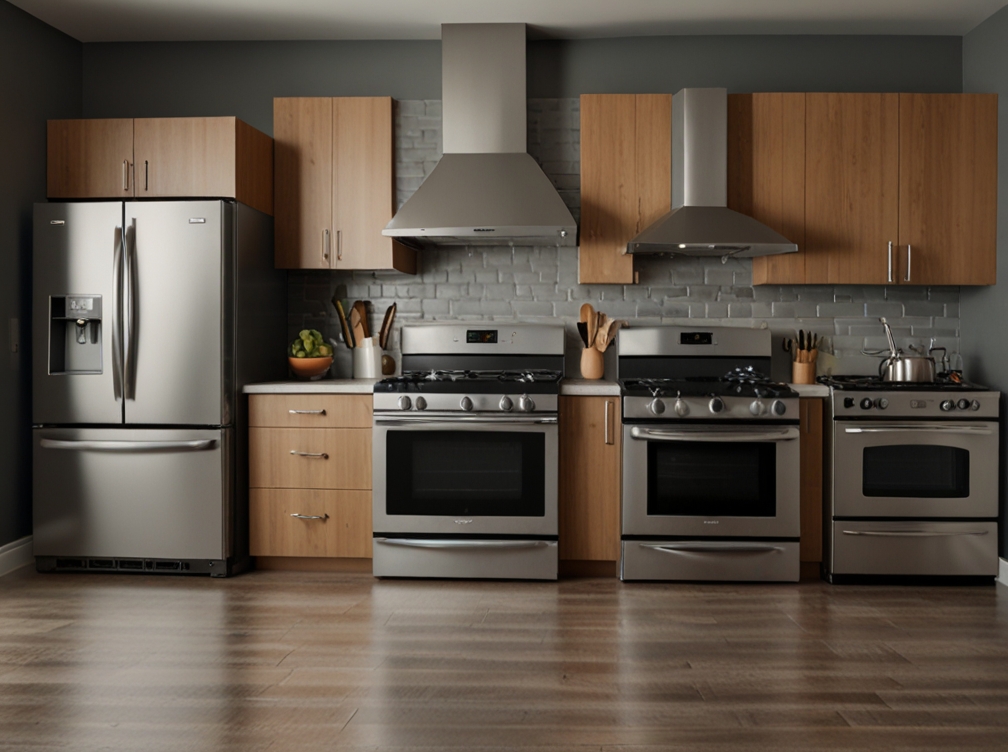
In an age where consumers are inundated with a vast array of products and brands, reliability becomes a critical factor in purchasing decisions. Manufacturers often tout the reliability of their products through various claims and statistics. However, the question remains: Can consumers trust these declared reliability characteristics? To answer this, we need to explore how reliability is measured, the potential biases in manufacturer claims, and alternative ways to assess product reliability.
Manufacturers typically declare the reliability of their products through metrics such as mean time between failures (MTBF), failure rate, warranty periods, and customer testimonials. These metrics are intended to provide consumers with an assurance of the product’s longevity and performance under normal usage conditions.
Mean Time Between Failures (MTBF):
MTBF is a common reliability metric used primarily for products with a long operational life, such as electronics and machinery. It estimates the average time a product operates before experiencing a failure. Higher MTBF values suggest better reliability.
Failure Rate:
The failure rate indicates the frequency of failures within a specific period, often expressed as a percentage. A lower failure rate implies higher reliability.
Warranty Period:
The duration of the warranty offered by a manufacturer is often seen as a proxy for confidence in the product’s reliability. Longer warranties typically suggest that the manufacturer expects the product to last longer without significant issues.
Customer Testimonials and Reviews:
Manufacturers may highlight positive customer feedback to bolster claims of reliability. These testimonials can provide anecdotal evidence of the product’s performance.